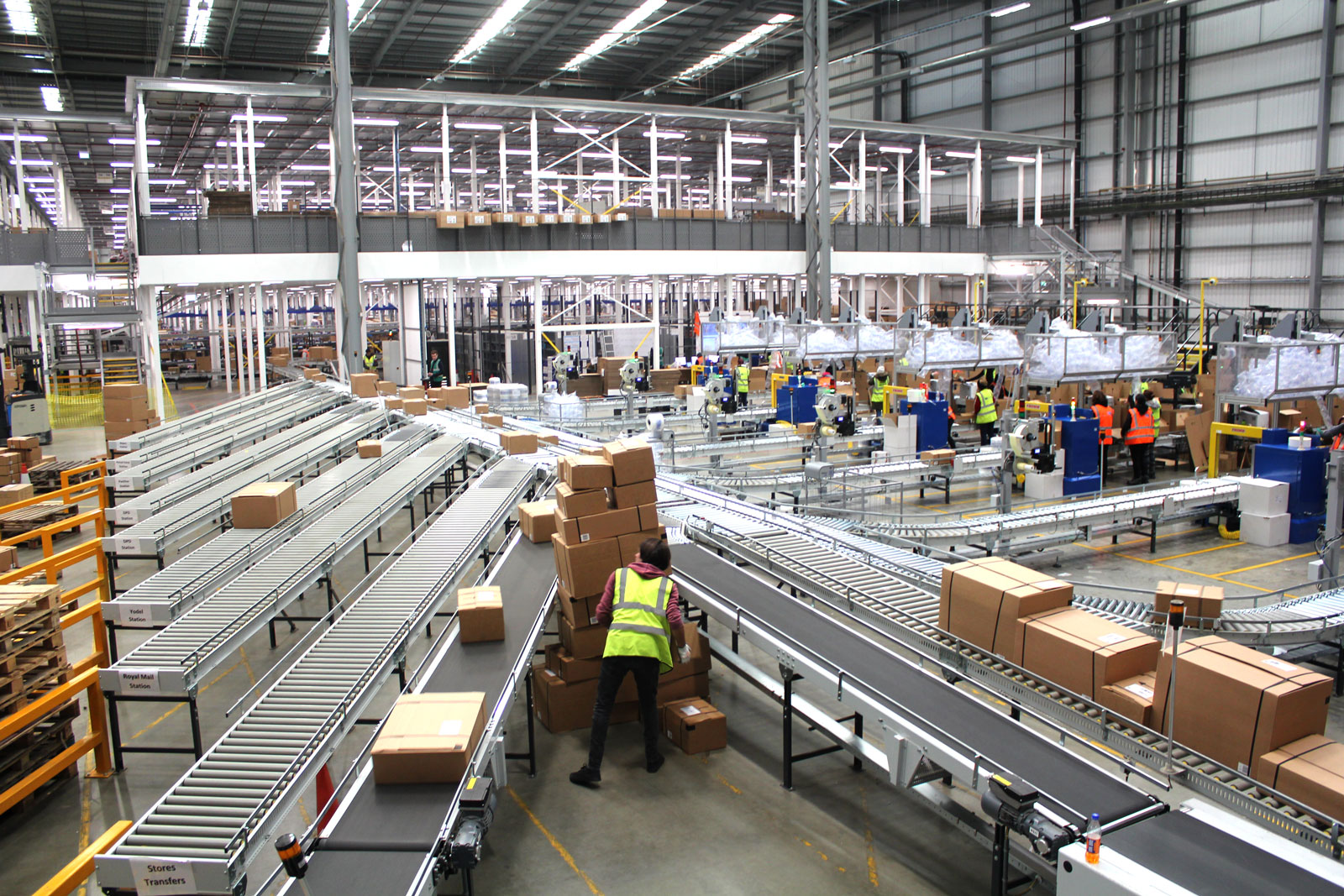
The Approach
Allied Storage brings a non-biased, activity based, industrial engineering approach to the development of each e-Commerce order fulfillment system. Allied Storage has the process improvement engineering experience and expertise to design high performance solutions. At the core of each solution is the system design and the strategic management software that provides real time control, visibility and operational insight.
Systems may be comprised of a single solution such as the pick and pack operation, or they may include all the operational functions from receiving to shipping.
Allied Storage engineers each system as a modular, flexible, scalable solution to accommodate changing activity profiles, average to peak capacity and future growth. Allied Storage guarantees successful system performance while creating a strong ROI:
- Reduce warehouse space requirements, fulfillment time, and labor
- Optimize material and information flow, processes, activities
- Increase throughput, accuracy and ergonomics
Pick to light
It is quiet in the e-commerce distribution center of Smyths Toys in Corby in Mid-England. The company, UK & Ireland’s largest toys retailer, copes with 25,000 orders a day. The new system which is in operation since the middle of 2016, is not under pressure now even with the volume of orders. The system has already proved itself last December, especially on Black Friday and Cyber Monday. “The original 400 people who had to process the order manually, are now down to 100 persons, says Stephen Kearney of Smyths Toys. ‘In peak periods over 30,000 orders per day are being processed by the system.” The solution from Allied Storage, is a mezzanine floor with conveyors, 2 spiral conveyors, a pick to light system with carton flow racks, adjustable pallet racking and Allied Storage own WMS.
Replenishment
E-commerce
Smyths offers the online buyer various delivery options like Next Day delivery, and Standard delivery. Around 4.30 p.m. the last orders are picked from the system which can still be processed. 70% of the orders are delivered as ‘standard service’, which means the article gets delivered between 2 and 4 days. 30% is next delivery.
Biggest advantages
Stephen about the biggest advantages brought by the system of Allied Storage. “Our replenishment process used to take up to many time in the past, which was at the expense of the production time. We have now much less stock, up to even 50% less even. We are a transactional warehouse, so our products have to go through quickly. We can store 1300 more SKU’s than before and this is because of the new replenishment system.”
Smyths has 78 stores in England. The dc in Corby is one of the regional dc’s for the shops and also the e-commerce warehouse for all of England. With the new replenishment and picking system Smyths has realized a massive productivity improvement. “Per shift we need half the people, from 280 per shift to 105. Because of the different way of working and the checks we also have less damage to the product and the customer satisfaction and delivery reliability have risen. Also the reaction speed of the activity on the website is much higher,” says Stephen.
Smyths grows considerably, especially online. Stephen believes that next year they need an extra mezzanine floor and the packing station will need an extension with extra lanes. Corby is for now the ideal location to handle the online growth. “We are close to the harbor of Felixstowe, from which a lot of supply comes.” There is also plenty of
labor, but in the peak period the company also employs temporary workers to cope. During the quiet period the company only needs the ‘skeleton staff’ of just 20 people.
Smyths is busy with the next improvements and is now building a new web site. It has to ensure a better return process. Stephen: “People can bring the goods back to the store and also the store stock will be integrated in our online supply. This has to prevent a minimal return goes to the dc in Corby.”
At the end of the tour through the company Lens van Rijn puts a map of the system on the table and the last adaptions are being discussed. The daily practice has shown that the process need a bit of extra conveyor length to be able to cope even better with the amount of boxes in the peak period, “Even if Smyths Toys would further grow to 40.000 orders a day, our system will be able to cope with it just fine.”